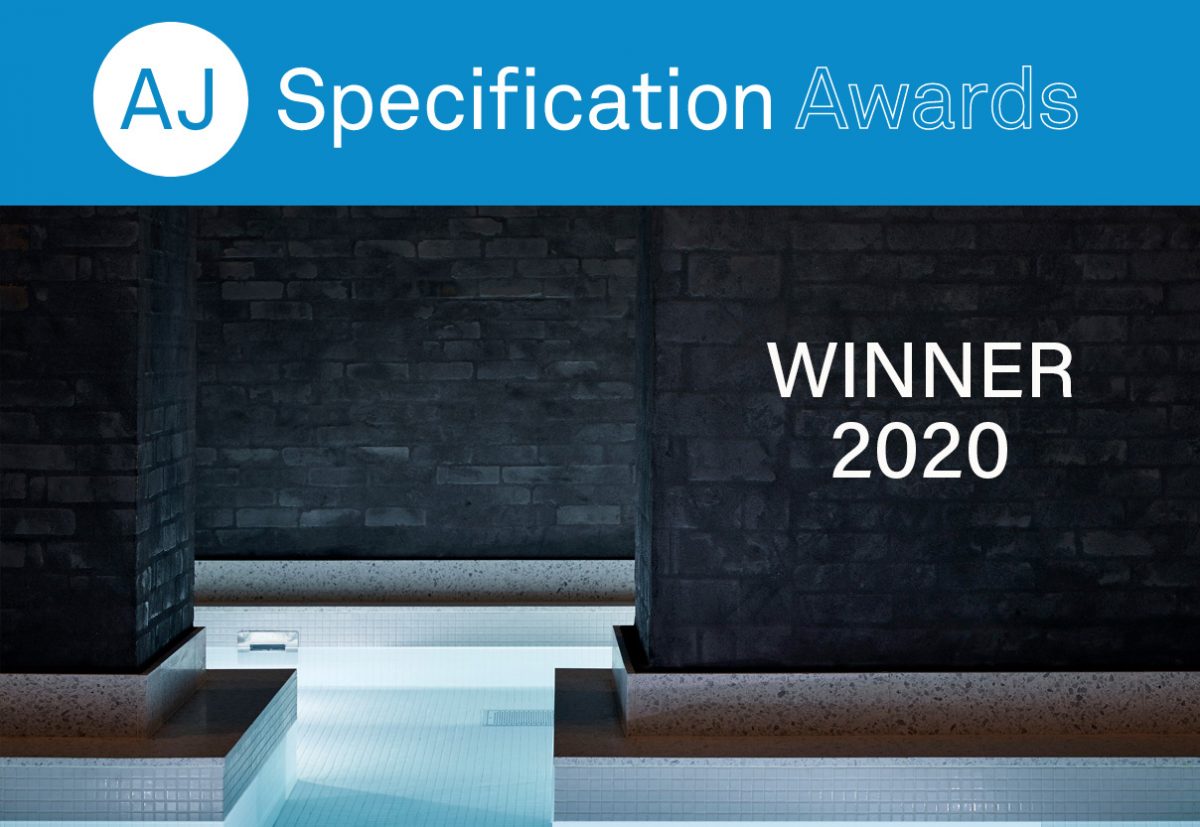
AJ Specification Award 2020 – Winner
Clayworks’ specialist clay finish Clay on Brick has won the Colour & Finishes category at AJ Specification Awards 2020.
The awards celebrate outstanding working relationships between UK architects, suppliers and manufacturers and the innovative and creative use of products and materials that results. ‘This project demonstrates an in-depth collaboration, with functional drivers giving the project a performance edge above its contenders’, said the judges.
The finish was developed in response to a challenge faced by Emil Eve Architects, who were researching how to protect and enhance porous and fragile historic brickwork, in a confined space, that would experience high temperatures and high levels of humidity.
The architects were designing a luxury spa in the basement of a large Victorian building, built originally as eight blocks of serviced flats between 1896 and 1905.
Without resorting to a lining, the architects sought a finish that would be not only high performing but aesthetically beautiful and sensitive to the building’s history and character. Emil Eve wanted to expose the texture of the brick while unifying the historic and damaged surfaces but to prevent damp reaching into the structure of the hotel.
Historic Brickwork Protection
Large areas of the walls in the refurbishment were rebuilt using reclaimed bricks, chosen to match the original in size and texture. Pointing was removed throughout and replaced with breathable lime mortar and breathable primer. The material that solved all of the critical challenges for the architects, however, and which avoided lining the space, was a Clayworks Clay Plaster.
Clay is one of the most ancient of building materials, traditionally dug up on-site and applied to interior walls. Over the past few years, Clayworks has led the way in re-imagining clay plasters as a contemporary solution to some of the significant problems facing the construction industry.
Clayworks has a long history in natural building and became authorities in lime, clay, and cob early this century, choosing to specialise in clay plasters in 2007. Several years of dedicated research and development, both in the field and in the laboratories of Bath University, resulted in a range of ready-mixed clay plasters, from very fine and silky, to extremely coarse and rustic. The plasters, all made in Cornwall, are being continually researched and developed by a dedicated, in house team of clay technicians.
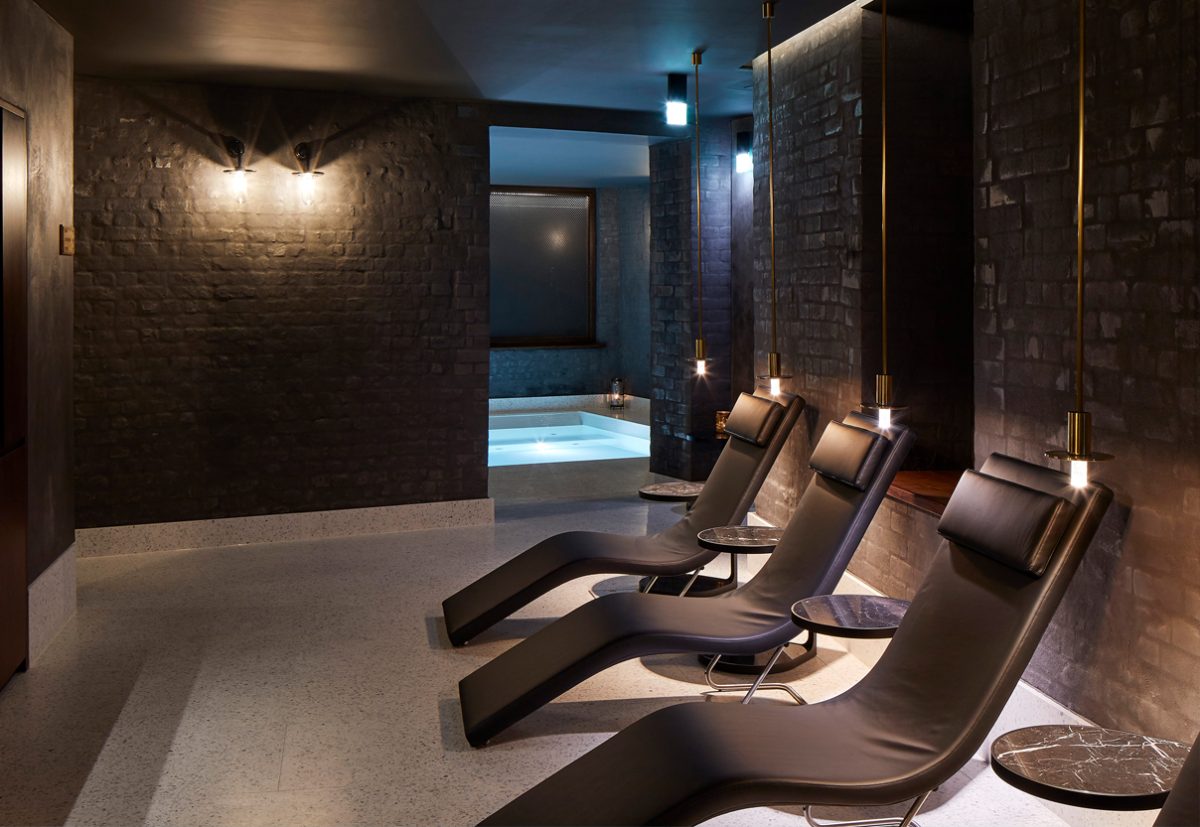
Materials Innovation
For Jiva Spa, an intensely pigmented black colour was created by Clayworks to meet the design specifications envisioned by Emil Eve. Black is a difficult colour to achieve with natural pigments, and the fine finish presented challenges that were overcome by developing a specific new texture and formulation.
While Clayworks tested materials in Cornwall, Emil Eve worked with the client, mechanical engineers, and other sub-contractors to model the airflow system in conjunction with inputting the known technical values of Clay Plasters.
After extensive testing with different textures and colours, including producing test panels on-site, Emil Eve developed a specification that overcame the technical challenge and achieved the client’s brief. Clayworks, in turn, collaborated closely with an approved, specialist plasterer, Steven Jendro, training him how to apply the new specialist plaster and its application methods.
The process of research, collaboration and trials had involved exploring several solutions to overcome the technical challenges. The successful variants (various combinations of different finishes) were applied as mock-up panels within the existing building to test the aesthetic and gain client approval.
Historical Building Renovations
Clay plasters do not change state when they dry – they simply set. They remain a raw material that absorbs and releases moisture, a quality known as hygroscopic. Unfired clays can absorb and desorb indoor humidity faster than any other building material and hence are ideal for a spa setting, where one of the challenges was to prevent moisture passing through the brickwork to other parts of the hotel and threatening the structural integrity of the building. (One of the reasons clay is often used with straw and wood building is its ability to wick moisture from the structural fabric of a building).
The collaboration of expertise has resulted in a clay plaster product, and application technique, that can be used for other historic buildings with important implications for the preservation of ancient brickwork.
Jiva Spa opened in March 2019, the first Jiva Spa in Europe. Jiva, meaning life force is inherently rooted in India’s ancient approach to wellness and inspired by traditional healing wisdom. So using healthy, natural materials was an essential consideration for brand sensitivity.
Sustainable Materials
Clay plasters are, by their very nature 100& natural, non-toxic, breathable, compostable and low carbon. By working with Clayworks, the architect could be sure that the materials would contain no synthetics, would not require the use of paint or other sealants and would have probably the lowest carbon footprint of any of the sealing options.
Manufactured in Cornwall, UK from abundant raw materials, they are amongst the most sustainable wall finishes [link to sustainability page] available. Recyclable, compostable, and containing no toxic ingredients, VOCs (harmful chemicals released during and after application) or synthetics they are healthy for the planet, the building fabric, and the occupants.
Made from readily available, naturally abundant materials, they require no processing, only blending. During this process very little energy is required, no water is used, and there are no waste materials. Clayworks Clay Plasters are packaged in Brown Paper sacks that contain no plastic. Hence there is no landfill waste.
All this means that they have very low embodied carbon and embodied energy, the carbon which is associated with the materials in the building. Embodied carbon normally encompasses both CO2 and other greenhouse gases, and includes emissions from all the extraction, transport and manufacturing processes required before products are ready at the factory for delivery to the customer – such an assessment is known as “cradle to gate”.
The Materials Council has concluded that up to 2.4KG of Carbon could be saved by using a clay plaster wall build up rather than Gypsum and Paint. Their calculations were based on Clayworks Clay Plasters and using data produced by the University of Bath.